The suspension system is one of the important components of a car. The automobile suspension system is a general term for connecting all the components between the vehicle body and the wheel. It is mainly composed of three parts: a spring, a damper and a steering mechanism. Its function is to transmit all the forces and moments between the wheel and the frame, and The impact load transmitted from the uneven road surface to the frame (or the vehicle body) is alleviated, and the vibration of the bearing system caused by the vibration is attenuated to ensure smooth running of the vehicle.
This article refers to the address: http://
The semi-active suspension refers to a suspension in which one or both of the suspension elastic element stiffness and the damper damping force can be adjusted as needed. Since the semi-active suspension is close to the active suspension in terms of control quality, and has a simple structure, low energy loss and low cost, it has great development potential.
Development status of semi-active suspension technology
The suspension can be divided into a passive suspension, a semi-active suspension and an active suspension depending on whether the damping and stiffness of the suspension vary with driving conditions. With the continuous improvement of living standards, users' requirements for car comfort are getting higher and higher, and the traditional car suspension system can no longer meet people's requirements. It is expected that the height of the automobile body, the rigidity of the suspension, and the damping of the damper can be automatically adjusted in accordance with changes in driving conditions such as the traveling speed of the vehicle and the road surface condition, thereby achieving an improvement in ride comfort.
In 1973, DACrosby and DC Karnopp of the University of California, Davis, first proposed the concept of semi-active suspension. The basic principle is: the suspension is composed of an adjustable stiffness spring or an adjustable damping damper, and the spring stiffness or the damping of the damper is adjusted according to a certain control law according to the feedback signal such as the acceleration response of the sprung mass. Achieve better damping effect. The semi-active suspension is divided into two categories: adjustable stiffness and adjustable damping. At present, in the research of semi-active suspension control, most of the research on damping control is carried out. The damper adjustable semi-active suspension can be further divided into a stepped adjustable semi-active suspension and a continuously adjustable semi-active suspension. The damping coefficient of the stepped adjustable semi-active suspension can only take several discrete damping values, and continuous The damping coefficient of the adjustable semi-active suspension can be continuously changed within a certain range.
Stage adjustable damper
The step-variable damper damping can be quickly switched between 2-3 steps, and the switching time is usually 10-20ms. The step-variable damper is actually a simpler control valve in the damper structure, allowing the flow area to be adjusted stepwise between maximum, medium or minimum. The rotation position of the rotary valve is controlled by the motor at the top of the damper, so that the damping of the damper changes between the "soft, medium and hard" three gears. The structure of the adjustable damper and its control system are relatively simple, but have certain limitations in adapting to changes in the driving conditions and road conditions of the vehicle. The adjustable damping of the continuously adjustable damper can be adjusted in two ways:
1. Throttle aperture adjustment
Early adjustable dampers were primarily oil dampers with real-time adjustment of the orifice. The damping is controlled by the stepper motor driving the damper's valve stem to continuously adjust the flow area of ​​the damper throttle valve. The throttle valve can be realized by a solenoid valve or other forms of driving valve. The main problem of this type of damper is that the throttle valve has a complicated structure and high manufacturing cost.
2. Damping fluid viscosity adjustment
It is a current research hotspot to use the continuously variable current or magnetorheological fluid as the damping fluid to achieve stepless change of damping. Under the action of an external electric field, the fluid material properties, such as shear strength and viscosity, will change significantly. As a damping fluid, it is only necessary to change the viscosity of the electric current to change the viscosity of the liquid. The damping force of the damper can be changed.
The damping of the eddy current damper can be continuously changed with the change of the electric field strength. There is no need for a high-precision throttle valve, the structure is simple, the manufacturing cost is low, and there is no vibration, shock and noise of the hydraulic valve, and no complicated driving mechanism is required. As a semi-active suspension actuator is a very good choice. However, there are some problems in electrorheological fluids, such as low yield strength, low temperature working range, high zero electric field viscosity, large difference in specific gravity between solid particles and base liquid in suspension, easy separation, sedimentation, and poor stability. , sensitive to impurities, etc. In order to make the current damper respond quickly and work reliably, the following problems must be solved: 1 Design a small-sized, lightweight, arbitrarily adjustable high-voltage power supply. 2 In order to ensure the normal working temperature of the electro-rheological fluid, there is a heat dissipation system. 3 insulation and packaging of high voltage power supply. Foreign companies such as Bayer in Germany and Lord in the United States have current damper products.
Magnetorheological fluid refers to a fluid whose rheological material properties change drastically under the action of an external magnetic field. By controlling the strength of the magnetic field, continuous, stepless adjustment of the damping of the magnetorheological damper can be achieved.
The magnetorheological damper has the similar feature of an electrorheological fluid damper, which is a liquid formed by suspending fine magnetic particles in an insulating medium. The viscosity increases with the increase of the applied magnetic field strength until it is semi-solid, and once the applied magnetic field disappears, it returns to its original state, and the whole process can be completed in milliseconds. The United States Lord Corporation, Ford Company, Germany BASF, etc. have invested heavily in research, such as the magnetorheological fluid MRX-126PD developed by Lord, the magnetorheological damper designed with single-rod piston cylinder structure has been used for large Semi-active suspension damping system for trucks.
The characteristics of electrorheological fluids and magnetorheological fluids are shown in the table below, and they all meet the requirements of automotive work. However, magnetorheological fluids are stronger than electro-rheological fluids in terms of yield stress, temperature range, plastic viscosity and stability.
Semi-active suspension control strategy
In recent years, domestic and foreign scholars have done a lot of research on semi-active suspension control methods. The control methods involve almost all branches of control theory. Many control methods such as canopy damping control, PID control, optimal control, adaptive control Neural network control, sliding mode variable structure control, fuzzy control, etc. have been applied to semi-active suspensions.
Canopy damping control
The ceiling damping control method is the earliest proposed control method. The control method was proposed by Professor D.KARNOPP of the United States and has been widely used in the early semi-active suspension. However, the canopy damping control only solves the comfort of the suspension system and does not solve the steering stability problem well. Therefore, the current research focuses on improved ceiling damping control methods.
best control
Optimal control is the most mature and widely used control method in theory. It can be divided into linear optimal control, optimal predictive control and H∞ optimal control. The linear optimal control is; the LQ (Linear-Quadratic) control theory is applied to the vehicle suspension system. The performance index function uses the system's state response and the input weighted quadratic form to ensure the dynamic stability of the controlled structure. Next, the linear quadratic regulation controller theory and the linear quadratic Gaussian control theory are applied to the vehicle semi-active suspension system to achieve optimal control. H∞ optimal control is an optimal control method for the minimum value of the output of the closed-loop system under the condition that the loops of the closed-loop system are stable, in the body quality, tire stiffness, damping damping system, vehicle structure, etc. When the uncertainty error is uncertain, the H∞ optimal control can make the vibration reduction control of the vehicle suspension system more robust.
Adaptive Control
The adaptive control has a parameter identification function, which can adapt to changes in suspension load and component characteristics, and automatically adjust control parameters to maintain optimal performance. The adaptive control methods applied to vehicle suspension systems mainly include model reference adaptive control and self-correction control. Self-correction control is a widely used one. The vehicle suspension damping damping system with adaptive control can improve the driving characteristics of the vehicle and is used in the chassis of Volkswagen AG.
Predictive control
The predictive control of the vehicle suspension system refers to passing the sensor; the road surface information in front of the vehicle is transmitted to the suspension device in advance, so that the adjustment of the parameters is synchronized with the actual demand. Predictive control can measure the information of the road ahead in advance by some method, so that the control system has enough time to take measures. Predictive control can be divided into two categories: one is to predictive control of the rear wheel suspension with the state information of the front wheel suspension; the other is to measure the state information of the road ahead during the driving of the vehicle, and use this information to carry out the front and rear wheel suspensions. Predictive control. The key to using predictive control is to obtain information that is accurate, undisturbed, and reflects the true condition of the road. Due to the time-varying of vehicle parameters and the influence of nonlinearity on system performance, it is difficult to study semi-active suspension with predictive control performance.
Neural Networks
Neural network is a new interdisciplinary subject that has developed rapidly in the past 20 years. It is a highly parallel nonlinear dynamic system composed of a large number of processing units (neurons) and a certain topological structure. Self-learning ability and large-scale parallel processing capability have broad application prospects in vehicle suspension system damping control.
At present, neural network control methods are increasingly used in specific environments and designs with multiple purposes using a fixed description. Automotive semi-active suspension systems have nonlinear characteristics. Conventional control strategies have certain limitations on nonlinear systems. Neural network control methods have broad application prospects in vehicle suspension control systems.
Sliding mode variable structure control
Sliding mode variable structure control is an important branch of control theory. It is suitable for linear or nonlinear systems. It is simple and easy to implement. It is highly robust to the uncertainty of model parameters and external disturbances. Sliding mode variable structure control is essentially a kind of special nonlinear control, and its nonlinearity is represented by control discontinuity. This control strategy is different from other controls in that the "structure" of the system is not fixed, but In the dynamic process, according to the current state of the system (such as the deviation and its derivatives), the system is continuously changed, forcing the system to move according to the predetermined "sliding mode" state trajectory. Because the sliding mode can be designed and compared with the object The parameters and disturbances are irrelevant, which makes the variable structure control have the advantages of fast response, insensitivity to parameter changes and disturbances, no need for online recognition of the system, and simple physical implementation.
Fuzzy control
Since the 1990s, fuzzy control has been applied to the control of automotive semi-active suspension systems. Fuzzy control is a new type of intelligent control technology. Compared with traditional control, its system is robust, especially suitable for nonlinear, time-varying and lag systems. Its biggest feature is that it allows the control object to have no precise mathematical model, and uses linguistic variables instead of digital variables. Similar to human intelligent behavior, fuzzy control is especially used due to the frequent changes of some parameters of the vehicle and driving under different road conditions.
Semi-active suspension development trend
The research and development of automotive suspension control system is an international frontier in the field of vehicle dynamics and control. The development of a suspension with safety, comfort, clean and efficient, energy-saving and intelligent control is the development direction of vehicle suspension system.
(1) Research on control strategies. The control of the semi-active suspension system involves almost all modern control theories and methods, but since each control method has its own advantages and disadvantages, the comprehensive application of multiple control methods is the development direction of semi-active suspension control.
(2) Research of the controller. The intelligent controller can automatically adjust the parameters of the suspension system according to information such as road conditions and vehicle vibrations, so that the vehicle has good ride comfort and stability.
(3) Development of controllable damper. Research and development of reliable ER and magnetorheological controllable dampers. The development of low-cost and high-reliability sensors, as well as high-performance microprocessors, is a prelude to the practical use of semi-active suspensions. At present, although the magnetorheological fluid has entered the commercialization stage, problems such as noise, durability, and stability are still used in the damper, and further research is needed.
This Car LED Light is IP56 waterproof rating, which could better protect the LED Bulb from the water or harsh environment. Energy Saving LED Light Bar could not only used in RV but also could use in many other application of Marine, Truck, Camper, motor home, Limousine, Travel trailer, caravan, boat etc.
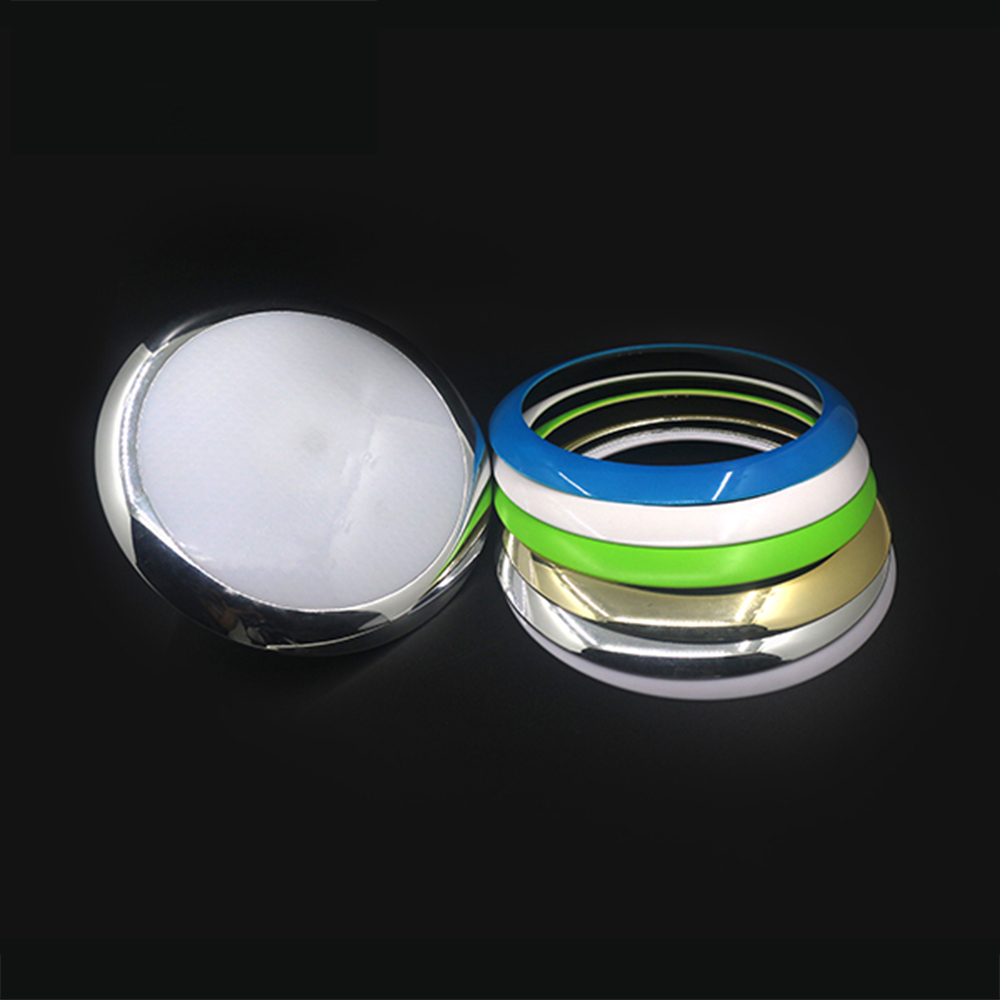
There are 12V DC 24VDC Voltage could be choose from. The Emitting Color could choose, including Red, White, Blue and etc. The Working life of the Ceiling Light is 30,000 Hours, which is a long time for use.
LED Light
LED Light,Car LED Light,RV Light,LED Lamp
YESWITCH ELECTRONICS CO., LTD. , https://www.yeswitches.com